Welcome to My Blog!
Before we dive into the content, I’d love for you to join me on my social media platforms where I share more insights, engage with the community, and post updates. Here’s how you can connect with me:
Facebook:https://www.facebook.com/profile.php?id=61571539990739
Now, let’s get started on our journey together. I hope you find the content here insightful, engaging, and valuable.
Table of Contents
Introduction
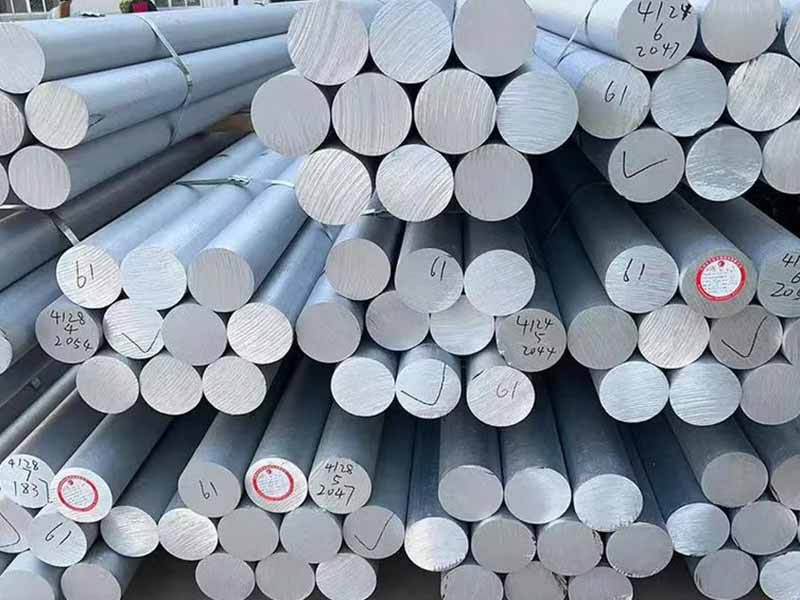
In the world of materials science and engineering, the choice between a solid aluminum rod and a hollow aluminum rod is a pivotal decision that impacts project outcomes across various industries. This comprehensive guide delves into the intricate comparison between these two forms of aluminum, exploring their distinct properties, applications, and advantages.
Understanding the nuances of solid aluminum rod versus hollow aluminum rod is crucial for engineers, designers, and manufacturers seeking optimal performance and efficiency. We will navigate through the material characteristics, structural differences, and practical applications, providing a detailed analysis to aid in informed decision-making.
Understanding Solid Aluminum Rod
A solid aluminum rod is a cylindrical bar of aluminum, characterized by its uniform, non-hollow cross-section. This solid structure imparts exceptional strength and rigidity, making it suitable for applications requiring high load-bearing capacity and structural integrity. Solid aluminum rod is manufactured through extrusion or drawing processes, resulting in a consistent and dense material. The inherent properties of aluminum, such as its lightweight nature, corrosion resistance, and thermal conductivity, are amplified in a solid form. This makes solid aluminum rod a preferred choice in demanding environments where durability and reliability are paramount.
Hollow Aluminum Rod: Properties and Applications
Conversely, a hollow aluminum rod features a central void, reducing its weight while maintaining a significant portion of its structural strength. This design optimizes the strength-to-weight ratio, making hollow rods ideal for applications where weight reduction is a critical factor. The manufacturing process of hollow aluminum rods involves extrusion with a mandrel, which creates the central void. This results in a material that offers a balance of strength and lightweight characteristics. Hollow rods are frequently used in aerospace, automotive, and other industries where minimizing weight is essential for enhancing performance and efficiency.
Comparative Analysis: Solid Aluminum Rod vs Hollow Rod
To provide a clear understanding of the differences between solid aluminum rod and hollow aluminum rod, we will examine their properties across several key parameters:
- Strength and Rigidity:
- Solid aluminum rod excels in applications requiring maximum strength and rigidity. Its solid structure provides superior resistance to bending and deformation under high loads.
- Hollow aluminum rod, while offering substantial strength, is inherently less rigid than its solid counterpart. However, it provides a favorable strength-to-weight ratio.
- Weight Considerations:
- Solid aluminum rod, due to its dense structure, is heavier than a hollow rod of the same dimensions.
- Hollow aluminum rod is significantly lighter, making it advantageous in applications where weight reduction is critical.
- Applications and Use Cases:
- Solid aluminum rod is commonly used in structural supports, machine components, and high-stress applications.
- Hollow aluminum rod is prevalent in aerospace components, automotive frames, and lightweight structural elements.
- Cost and Manufacturing:
- Solid aluminum rod manufactoring is generally simpler, which can effect cost.
- Hollow aluminum rod manufactoring processes are more complex, and therefore can increase cost.
- Thermal Properties:
- Due to the mass of the solid aluminum rod heat transfer will be different than in a hollow rod.
- hollow rods will transfer heat differently due to its shape.
Detailed Property Comparison Table
To further illustrate the distinctions between solid aluminum rod and hollow aluminum rod, consider the following comparative table:
Property | Solid Aluminum Rod | Hollow Aluminum Rod |
---|---|---|
Strength | High | Moderate to High |
Rigidity | High | Moderate |
Weight | Higher | Lower |
Applications | Structural supports, heavy machinery | Aerospace components, lightweight frames |
Load Bearing | Excellent | Good |
Manufacturing Complexity | Lower | Higher |
Thermal Conductivity | High | Moderate |
Applications of Solid Aluminum Rod
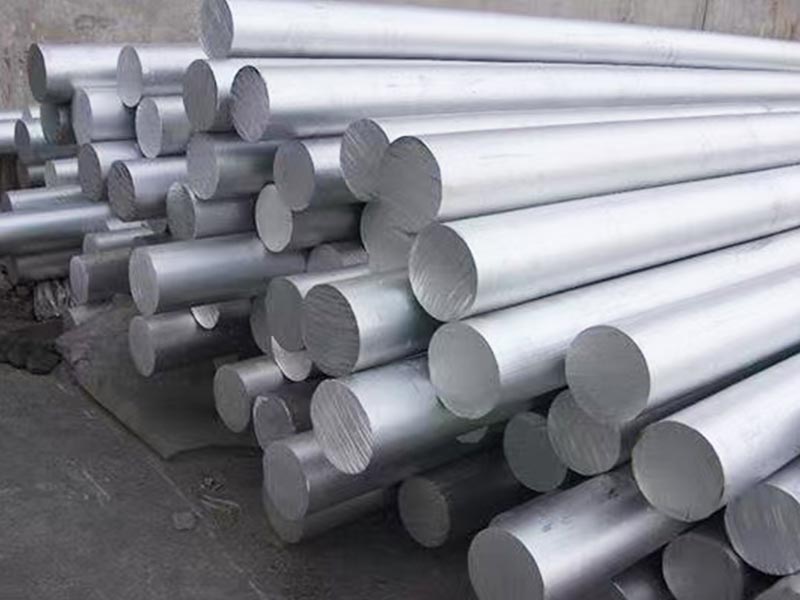
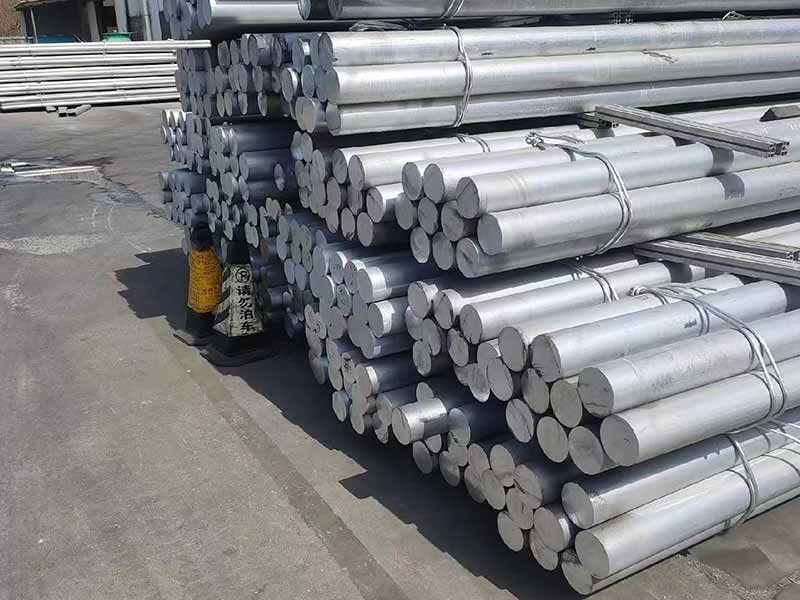
The robust nature of solid aluminum rod makes it indispensable in various industrial applications.
- Structural Supports: In construction and engineering, solid aluminum rod is used for its high load-bearing capacity in support beams and columns.
- Machine Components: Its strength and durability make it ideal for manufacturing machine parts, such as shafts, axles, and fasteners.
- Heavy Machinery: In industrial settings, solid aluminum rod is used in the construction of heavy machinery components that require high strength and resistance to wear.
Applications of Hollow Aluminum Rod
Hollow aluminum rod finds its niche in applications where weight reduction is paramount.
- Aerospace Components: In aircraft construction, hollow rods are used to minimize weight, improving fuel efficiency and performance.
- Automotive Frames: Hollow rods are used in automotive frames to reduce vehicle weight, enhancing fuel economy and handling.
- Lightweight Structures: In architectural and design applications, hollow rods are used to create lightweight yet sturdy structures.
Material Selection Considerations
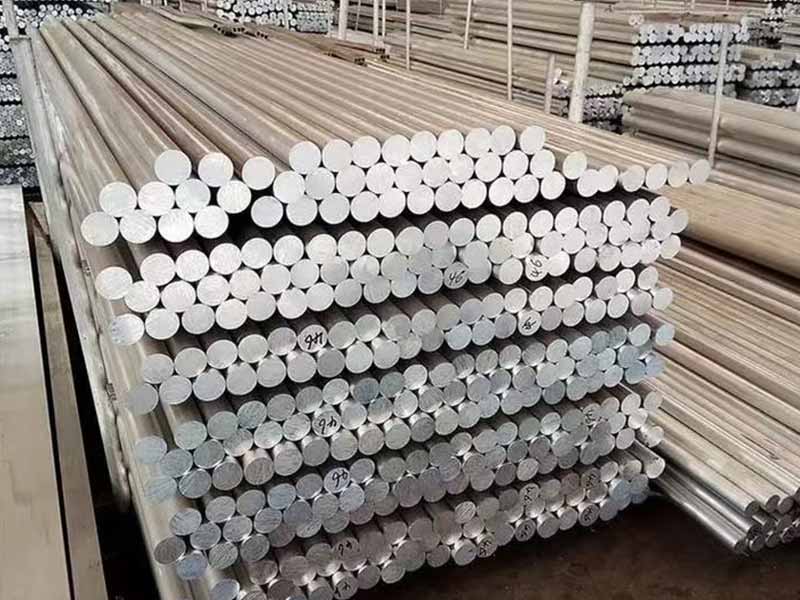
The decision between solid aluminum rod and hollow aluminum rod hinges on the specific requirements of the application. Factors such as load-bearing capacity, weight constraints, and environmental conditions must be carefully evaluated.
Load Requirements: If the application demands high load-bearing capacity and structural integrity, solid aluminum rod is the preferred choice.
Weight Optimization: For applications where weight reduction is crucial, hollow aluminum rod offers a favorable balance of strength and lightweight characteristics.
Environmental Factors: Aluminum’s inherent corrosion resistance makes both solid and hollow rods suitable for outdoor and harsh environments.
Conclusion
In summary, the selection between solid aluminum rod and hollow aluminum rod is a critical decision that impacts project performance and efficiency. Solid aluminum rod offers exceptional strength and rigidity, making it ideal for high-load applications. Conversely, hollow aluminum rod provides a favorable strength-to-weight ratio, catering to applications where weight reduction is essential. By understanding the distinct properties and applications of each material, engineers and designers can make informed decisions to optimize their projects. Therefore, understanding the properties of each type of Aluminum rod is very important.
FAQ
What are the primary advantages of using a solid aluminum rod?
The primary advantages of using a solid aluminum rod include its high strength, rigidity, and excellent load-bearing capacity. These properties make it suitable for applications requiring structural integrity and durability.
In what applications is a hollow aluminum rod most beneficial?
Hollow aluminum rod is most beneficial in applications where weight reduction is a critical factor, such as in aerospace components, automotive frames, and lightweight structures.
How does the strength of a solid aluminum rod compare to that of a hollow aluminum rod?
A solid aluminum rod generally exhibits higher strength and rigidity compared to a hollow aluminum rod of the same dimensions. However, hollow aluminum rods offer a more favorable strength-to-weight ratio.
What manufacturing processes are used to produce solid and hollow aluminum rods?
Solid aluminum rod is typically manufactured through extrusion or drawing processes. Hollow aluminum rod is produced through extrusion with a mandrel to create the central void.
Are aluminum rods resistant to corrosion?
Yes, aluminum is inherently corrosion-resistant, making both solid and hollow aluminum rods suitable for outdoor and harsh environments.
When deciding between these two types of rods, what are the most important things to consider?
The most important things to consider are the load requirements, weight restrictions, and the environment the rods will be placed in.